Automobilwerk : Von dort bekommt der VW ID.3 seine Komponenten her
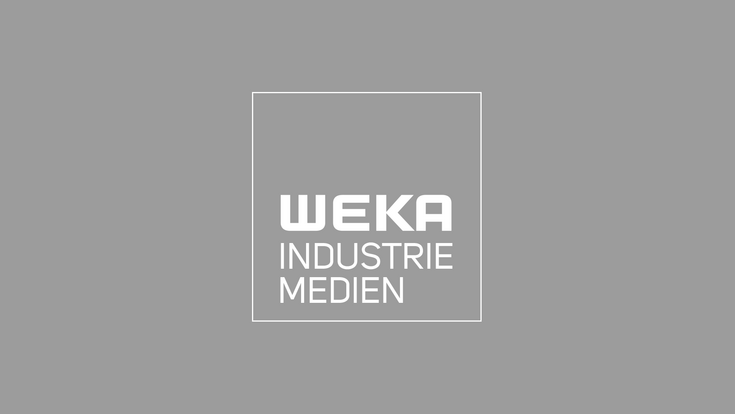
Zusammengebaut wird das rein batterieelektrische Modellfahrzeug ID.3 im sächsischen Zwickau. Die Vorserienproduktion ist bereits angelaufen. Die Komponenten für die vollelektrische Fahrzeugserie stammen zum guten Teil aus aus dem Volkswagenwerk Braunschweig. Der E-Antrieb kommt aus Kassel, der Standort Salzgitter liefert den hessischen Kollegen Rotor und Stator zu und andere Werke steuern Guss- oder weitere Bauteile bei. "Wir bauen unsere Werke konsequent für die neuen Elektromobilen Produkte um", sagt Thomas Schmall, Vorstandsvorsitzender der Volkswagen Group Components. "Dabei spezialisieren wir einzelne Standorte und nutzen gleichzeitig die Synergien der Verbundfertigung in der Konzern Komponente."
Das Werk der Konzern Komponente in Kassel liefert die elektrischen Antriebe und zudem Plattformteile für den ID.3. Neben dem Direktschaltgetriebe DSG, für das Kassel seit Produktionsbeginn vor 16 Jahren bekannt ist, werden künftig vor allem E-Antriebe für den Modularen E-Antriebs-Baukasten (MEB) gefertigt. Zusammen mit Teilen aus den Komponentenwerken Salzgitter, Poznań und Hannover werden am Standort Kassel alle Bauteile zum E-Antrieb zusammengefügt.
Kassel fertigt dabei die E-Antriebe für alle MEB-Fahrzeuge für Europa und Nordamerika. Die Produktion der Vorserienantriebe ist bereits erfolgreich angelaufen, künftig werden bis zu 500.000 Einheiten pro Jahr das Werk verlassen. Kassel kooperiert eng mit dem chinesischen Werk Tianjin, wo parallel der E-Antrieb für den chinesischen Markt produziert wird. Gemeinsam werden die beiden Werke ab 2023 pro Jahr bis zu 1,4 Millionen E-Antriebe produzieren.
Die Volkswagen Group Components ist damit künftig weltweit einer der größten Hersteller von E-Antrieben für Fahrzeuge. Neben dem E-Antrieb werden in Kassel zudem tragende Bau- und Karosserieteile für den ID.3 gefertigt: Teile des ultrafesten Rahmen für den Batteriekasten, Dämpferaufnahmen, Querträger und der Tunnel. Die Kasseler Plattformteile werden anschließend im Werk Zwickau zur fertigen Fahrzeugkarosse verbaut.
Rotor und Stator aus Salzgitter
Das Komponentenwerk Salzgitter hat sich im Rahmen der Transformation zur E-Mobilität zusätzlich zur konventionellen Motorenfertigung auf die Produktion von Rotor und Stator, zwei elementaren Bauteilen des E-Antriebs, spezialisiert. Neben Otto-, Diesel- und CNG-Antrieben werden hier pro Tag künftig bis zu 2.000 Einheiten Rotor und Stator produziert. Um diese hohe Stückzahlen zu realisieren, wird in der Statorfertigung eine selbstentwickelte neue Hairpin-Technologie eingesetzt. Das ermöglicht verbesserte Leistungsdaten bei kürzeren Fertigungszeiten.
Salzgitter steht zudem exemplarisch für den Transformationsprozess der Konzern Komponente: Die Volkswagen Group Components hat innerhalb der Volkswagen AG die End-to-End-Verantwortung für die Batterie, von der Forschung bis zum Recycling, übernommen - und der Standort Salzgitter übernimmt darin entscheidende Abschnitte: Im Center of Excellence (CoE) wird Batteriefachwissen aufgebaut und noch in diesem Jahr eine Pilotanlage zur Batteriezellfertigung eröffnet. 2020 folgt die Pilotanlage für das Batterierecycling. In beiden Pilotanlagen sollen Kompetenz und Industrieprozesse aufgebaut werden.
Batteriesystem aus Braunschweig
Am Standort Braunschweig wird das Batteriesystem für den ID.3 gefertigt. Eigens für die Produktion des äußerlich an eine Schokoladentafel erinnerndes Batteriesystem wird eine neue Halle errichtet - in der Fläche so groß wie neun Fußballfelder. Die Eröffnung ist für das vierte Quartal 2019 vorgesehen. Rund 2.000 Einheiten werden hier künftig täglich gefertigt und zur Fahrzeugproduktion nach Zwickau geliefert. Bereits seit 2013 baut der Standort Braunschweig seine Batteriekompetenz kontinuierlich aus, sowohl in der Entwicklung kompletter Systeme als auch in der Fertigung. Unter anderem werden hier Batteriesysteme für aktuelle Elektro- und Hybridfahrzeuge der Marke Volkswagen sowie für die Lkw von Scania und MAN produziert.
Die langjährige Erfahrung und das Know-how sind auch in das neueste Batteriesystem für den MEB eingeflossen. Aktuell werden die bereits hergestellten MEB-Batteriesysteme einer mehrwöchigen Härteprüfung unterzogen und auf Herz und Nieren getestet. Die Ergebnisse fließen anschließend in die weitere Entwicklung ein. Der Standort Braunschweig stellt zudem Fahrwerkskomponenten her und montiert die Vorder- und Hinterachsen. Dazu zählen u.a. die Schweißgruppen und Lenksysteme, aber auch die Antriebsgelenkwellen aus dem Standort Fahrwerk Wolfsburg.