Leichtmetall : So grün war eine Gießerei noch nie
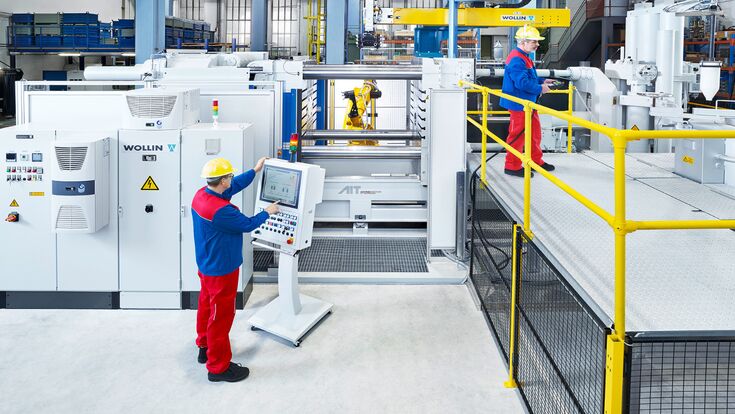
Die Demonstratoranlage der "Grünen Gießerei" im Leichtmetallkompetenzzentrum Ranshofen
- © AIT/LKREin typisches Herstellungsverfahren für Leichtmetall ist das Gießen. Der Prozess leidet an Energieverlusten, weil die einzelnen Produktionsschritte Schmelzen, Gießen, Wärmebehandlung und mechanische Bearbeitung entkoppelt in eigenen funktionellen Inseln stattfinden. Durch unterschiedliche Energieeffizienzmaßnahmen kann der Energiebedarf um bis zu 50 Prozent reduziert werden. Der Rest wird durch erneuerbare Energieträger (Biogas, Holzgas, Ökostrom, grüner Wasserstoff) gedeckt. Dadurch kann eine vollständige Dekarbonisierung erreicht werden.
Gießerei für Testzwecke
Im Leichtmetallkompetenzzentrum Ranshofen (LKR) baut das Austrian Institute of Technology (AIT) eine Gießerei für Testzwecke. "Mit der Green Demo-Foundry 4.0 wollen wir zeigen, dass für energieeffiziente Gießereien der Zukunft ein ganzheitlicher Ansatz von oberster Priorität ist, der Stoffströme und Energie berücksichtigt", erklärt Simon Frank vom LKR.
Der Fokus liegt auf einer verbesserten Energierückgewinnung und -nutzung mithilfe eines neuartigen bi-direktionalen Hochtemperatur-Wärmeverteilsystems, einer energie- und qualitätsoptimierten Gussform der nächsten Generation und abwärmeintegrierten Wärmebehandlungsöfen. Diese sogenannten Drehherdöfen für das Lösungsglühen von Aluminium-Druckgussbauteilen bei etwa 500°C hat die Hofmann Wärmetechnik aus Hellmonsödt entwickelt.
Öfen aus dem Mühlviertel
"Der Vorteil dieses Ofentyps liegt in der sehr energiesparenden Bauweise. Der elektrisch beheizte Ofen ist zylinderförmig ausgeführt und kann über einzelne kleine Ofentüren automatisiert mit einem Roboter beschickt werden", erklärt der technische Vertriebsleiter Markus Auer. Der Chargentransport im Ofen erfolgt über ein Karussell, das auf mehreren, übereinander angeordneten Ebenen Chargenteile aufnehmen kann."„Hier liegt der Vorteil auf der Hand: Es müssen keine zusätzlichen Vorrichtungen wie Glühkörbe erwärmt werden, sondern nur die Chargen selbst", ergänzt Auer.
Abwärmenutzung
In einem zweiten Arbeitspaket erarbeitet das AIT gemeinsam mit Hofmann ein verbessertes Heiz-Kühl-Konzept, das eine Abwärmenutzung aus dem Gussprozess erlaubt. Das neuartige Wärmeverteilsystem transportiert Abwärme mittels Thermoöl und Druckwasser zu den Öfen, in denen Aluminiummasseln vorgewärmt werden können. Dadurch benötigt das Einschmelzen um bis zu 30 % weniger Energie. "Auch der Auslagerungsofen, der für das Härten der geglühten und abgeschreckten Druckgussbauteile bei 200°C benötigt wird, kann über einen Wärmetauscher mit der Abwärme aus dem Gießprozess beheizt werden", sagt Markus Auer.
Intensive Entwicklungsarbeit
Simon Frank über den aktuellen Stand des Projekts: "Derzeit arbeiten wir intensiv an der Entwicklung und Integration der Wärmebehandlungsöfen, des Prozessleitsystems inklusive Hochtemperatur-Wärmeverteilsystem zur Erfassung, Dokumentation und Steuerung der Energieströme sowie des Designs der innovativen Gussform."